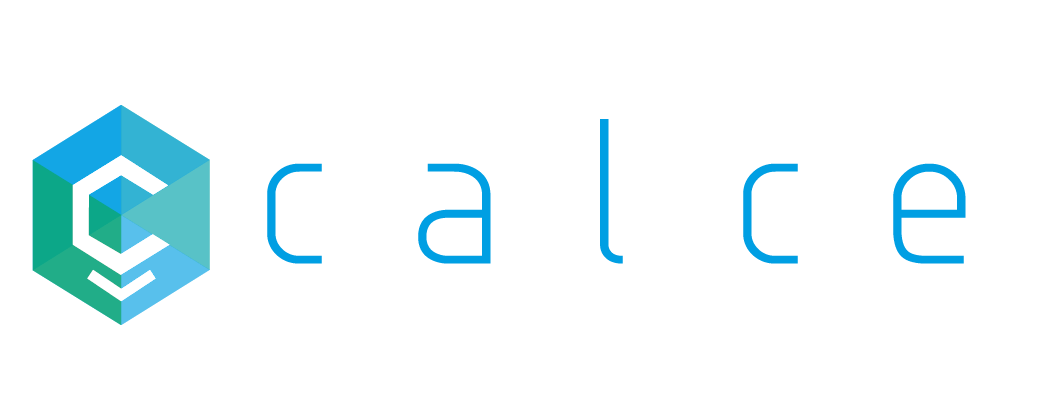
La innovación de ingeniería permite modernizar el proceso de generación de las prótesis, disminuyendo los costos y tiempos de ejecución, aumentando el acceso a la tecnología incluso en zonas remotas del país.
Tradicionalmente, las prótesis para personas con extremidades amputadas se confeccionaban de forma artesanal, con moldes de yeso, en un proceso que duraba varias semanas. El potencial de usar impresoras 3D de alta precisión para ofrecer una tecnorehabilitación alternativa más eficiente llevó al Instituto Sistemas Complejos de Ingeniería (ISCI) a apoyar a Calce, una propuesta innovadora que cambia la vida de los pacientes con tecnología digital de punta, supliendo el déficit de profesionales protesistas, descentralizando la producción de insumos de rehabilitación, y modernizando la ortopedia a nivel nacional con productos de vanguardia diseñados y producidos en Chile.
Calce surge en 2017, compuesto por un equipo multidisciplinario de profesionales de la salud, ingeniería y diseño. Desde su origen el emprendimiento buscó la generación de conocimiento y experiencia en tecnologías de impresión y escaneo 3D, para su aplicación creativa e innovadora en productos de rehabilitación, con tiempos más cortos que la fabricación de prótesis tradicionales. Otro de sus objetivos es universalizar el diseño de las soluciones de excelencia entre quienes las necesitan, impactando en sus experiencias cotidianas.
En primera instancia, el miembro amputado es escaneado en tan solo 10 segundos, logrando una lectura morfológica precisa de la extremidad. Este proceso puede ser realizado en distintos centros médicos del país que cuentan con la tecnología. Luego, se genera un modelo digital que se usa como base para que una impresora 3D construya la cavidad, que es la pieza más importante de la rehabilitación, ya que une la extremidad residual de la persona con el resto de su prótesis. Esta se imprime capa por capa de forma controlada, generando un producto de material firme y resistente, en un plazo máximo de cinco días hábiles.
“Si la cavidad no está bien hecha, entonces el paciente no usará la prótesis, desperdiciando importantes recursos económicos. Gracias a nuestra investigación sabemos que las piezas deben diseñarse para disminuir el dolor de los usuarios a través de recovecos, alivios, y presiones, respetando siempre el criterio del profesional protesista a cargo, a través de un software especializado disponible en internet. También, gran parte de la investigación inicial se dedicó a explorar las decenas de alternativas de materialidad, así como la correcta forma de imprimirlas en 3D, para que las cavidades tuviesen la resistencia necesaria”,
explica Andrés Sanhueza, Gerente General de Calce.
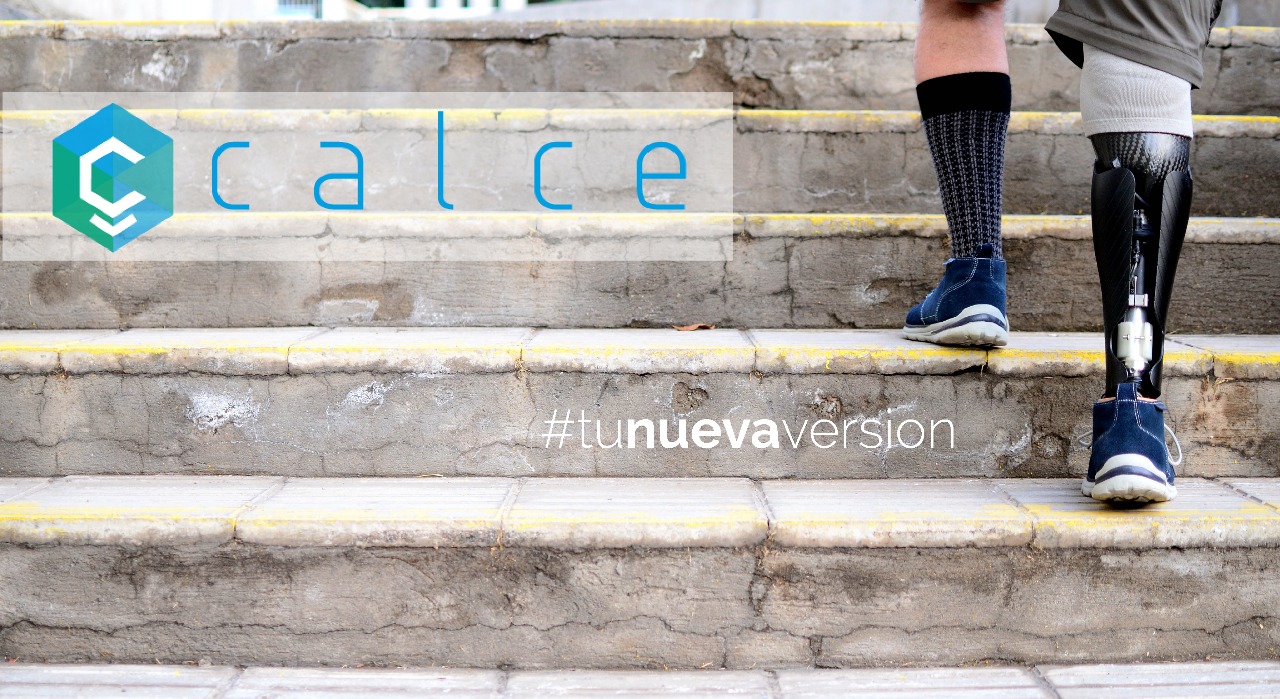
Actualmente, más de 200 personas están caminando con una prótesis con Cavidad 3D diseñada por Calce en su proceso de rehabilitación. La meta para 2019 es alcanzar a 400 pacientes, incluyendo dos nuevos puntos de atención en Punta Arenas y Concepción, que es un primer paso en el proceso de descentralización del acceso a prótesis de fabricación más rápida y menos costosas.
Comunicaciones ISCI